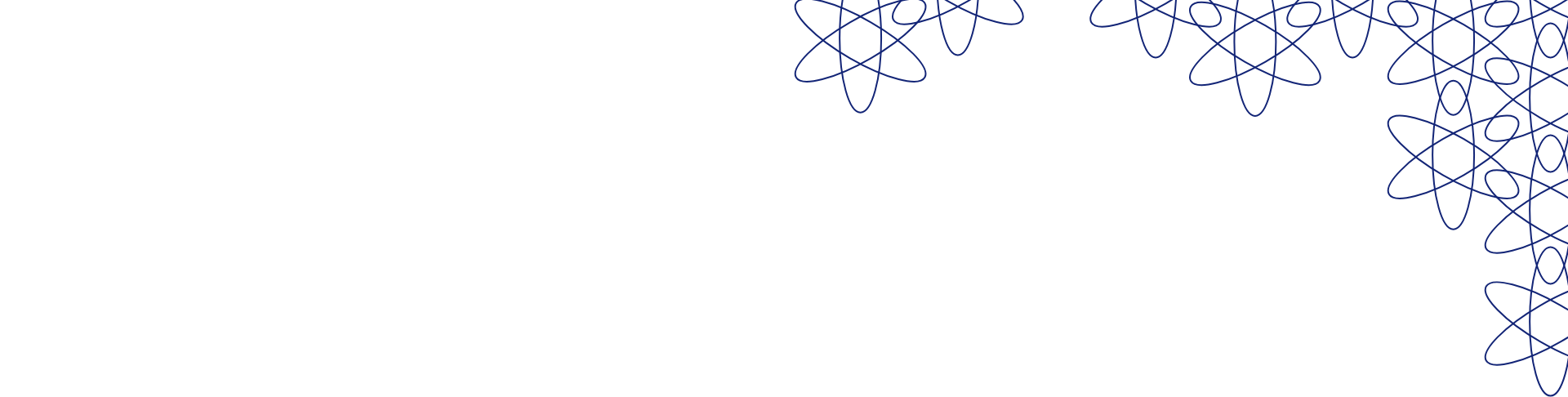
Sunday |
|
13:30 – 17:30 | Registration |
17:30 – 20:00 | Reception, Registration, Mingle |
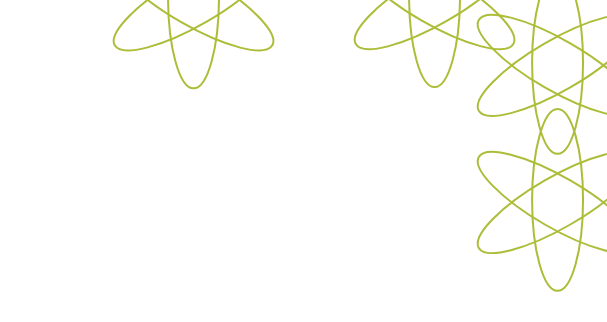
Wednesday – visit our facilities!
8:30 – 10:00 | Lessons Learned |
10:30 – 12:00 | Breakout Session I and II |
13:30 – 17:00 | ESS + MAX IV visits |
19:00 – 22:30 | Banquet Dinner |
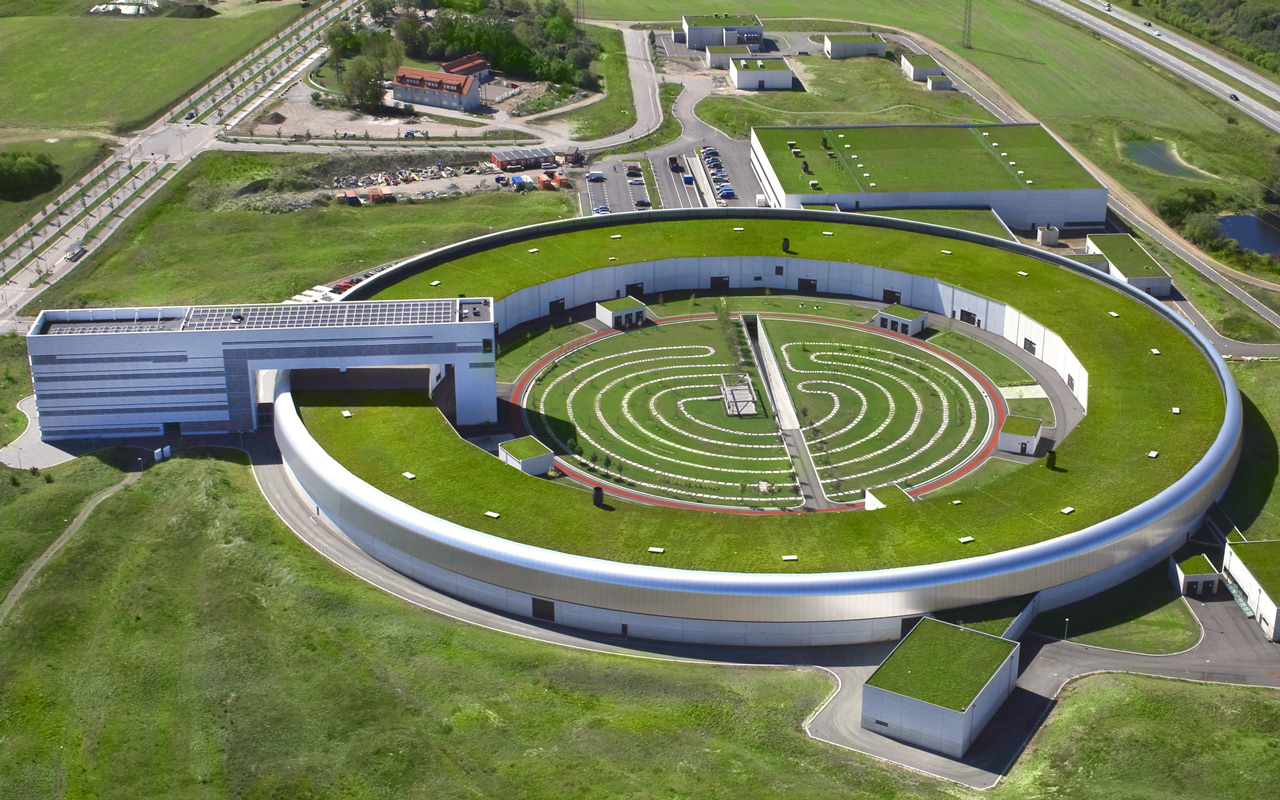
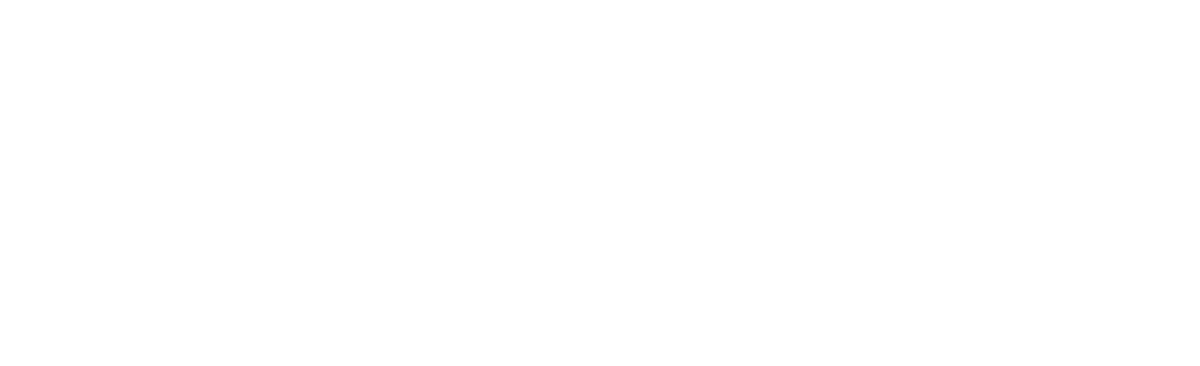
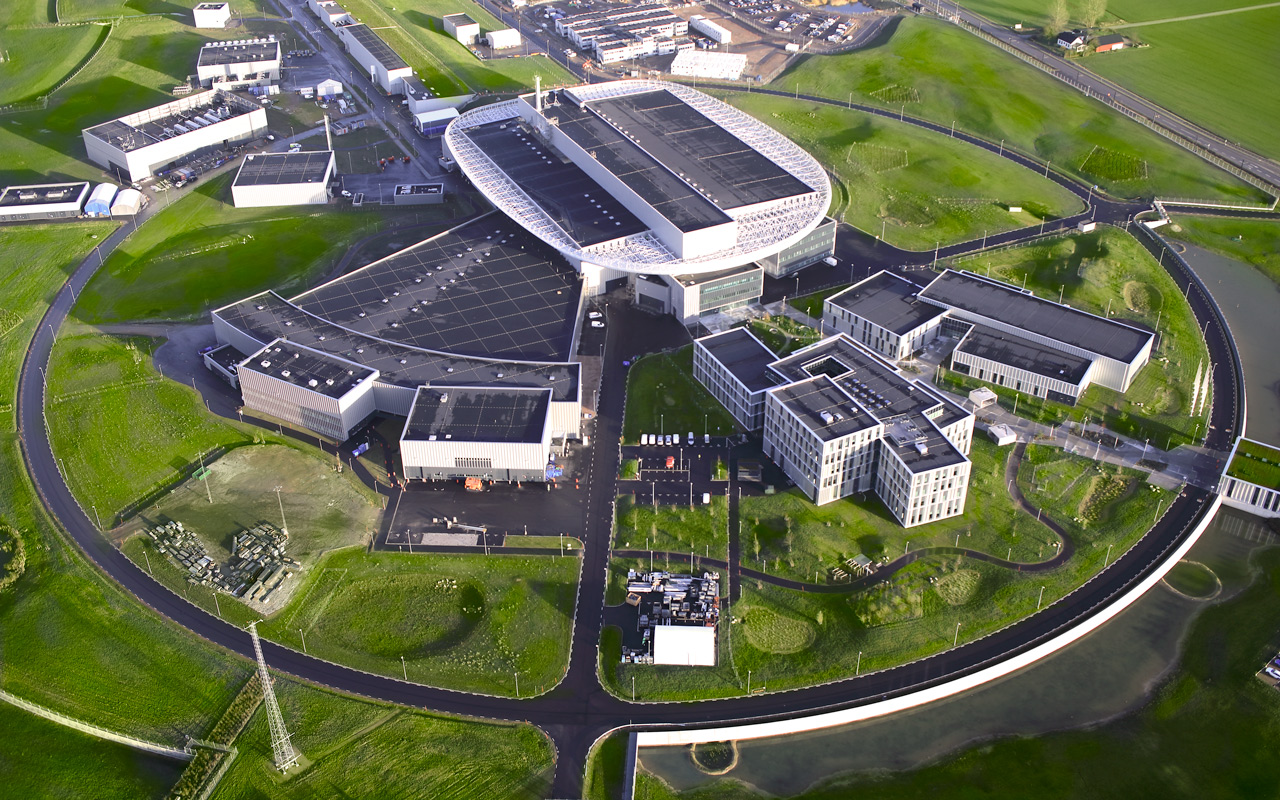
Thursday
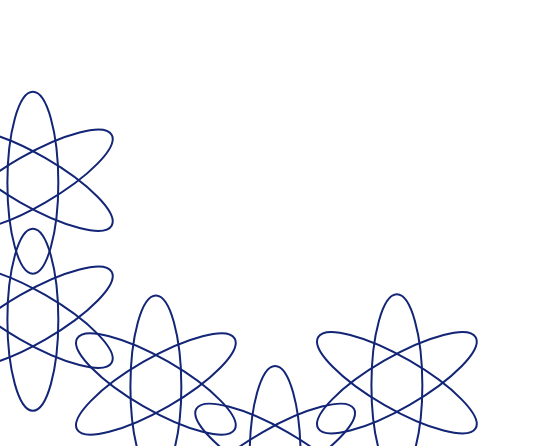
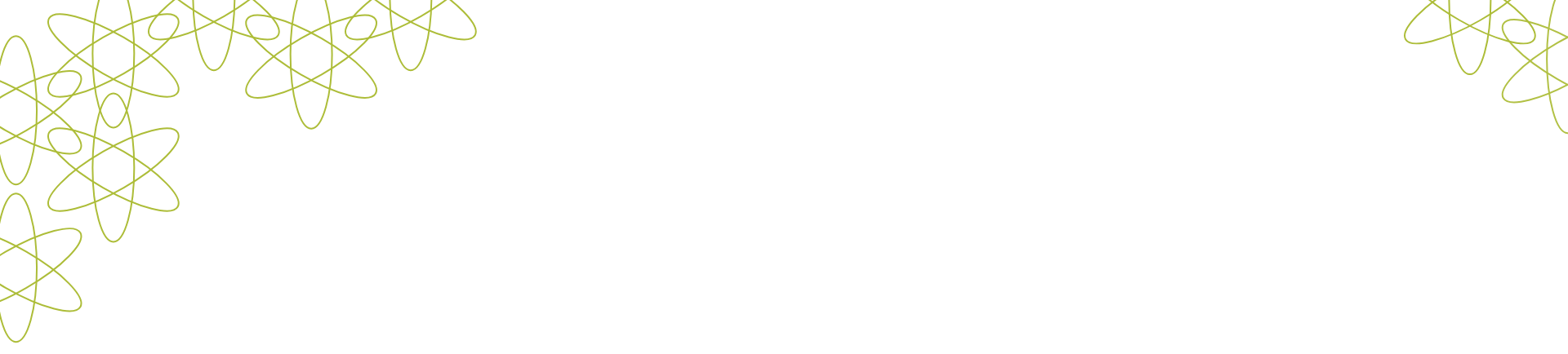
See you at the ARW 2024!
ESS and MAX IV are excited to welcome you to
Helsingborg, Sweden, at the SEA U conference centre from 2024-06-23 until 2024-06-28!
Please pre-book these dates and then JOIN US in 2024 in Sweden at a beautiful and stimulating venue overlooking the Öresund Strait which separates Sweden and Denmark!
Join ARW 2024 Now!
Registration is now open - on Indico.
For VISA guidance please check here.
General Inquiries: arw2024@ess.eu

At some point, all systems fail. When working with complex systems we often use well established techniques to mitigate failures by using corrective, preventive, and predictive maintenance techniques. We also try to mitigate failure risks using different methodologies such as failure mode and effects analysis (FMEA). Different methods may work better for different systems and some methods work better for single systems vs complex integrated systems. This session will focus on:
- Differences in analysis techniques in individual systems versus complex/integrated systems
- Unintended consequences related to integrating systems
- Reaction vs planning after an unexpected failure
- Systems integration issues during commissioning
When building or upgrading new accelerator facilities, we make decisions that can impact the quality of the design, installation, and, ultimately, the reliability of a facility. Procurement practices, outsourced design and development, environmental conditions, and space limitations can affect the end product and cause project delays and budget overruns if contracts and requirements are not well-specified. In this session, we will explore if your lab considers reliability during the procurement and installation of new and upgraded facilities and how reliability standards and maintainability are retained throughout the project lifecycle and after handover to operations.
Machine Learning (ML) and Artificial Intelligence (AI) are increasingly important concepts which can be applied to Accelerator control systems, and the analysis of accelerator performance and operations. Complex and powerful machines need reliable systems, and reliable operation to deliver their design objectives. ML & AI are emerging tools, which can be used to increase performance and achieve availability objectives.
This session aims to explore:
- Existing examples of AI / ML being used on operational systems, with the experiences and lessons learned.
- What kinds of systems?
- What kind of information is being captured?
- Good / bad points?
- Scope for the application of ML into systems that are intended to be used on a daily basis, assisting operations with their day-to-day role.
- What assistance can be given to operations?
The maintenance of accelerator-related equipment is central to maintaining high uptime of our facilities. On the one hand, the general trend today is to reduce the amount of maintenance time spent on each piece of equipment. On the other hand, in an increasingly data-driven world, the number of devices and their complexity continue to grow. Predictive maintenance could be part of the solution to keep operations running cost effectively in a time effective manner.
- Do we need to update our maintenance methodology depending on the type of equipment?
- Does the maintenance strategy take advantage of the huge data that can be made available in our control system?
- Is Reliability Centered Maintenance adapted to different types of facilities (light sources, medical facilities, facilities with low staff or expertise)?
- Sharing examples, self-developed or commercial tools are more than welcome
Facility reliability is the ability of an organization to operate while ensuring their equipment continues to perform its function consistently over a specified period and within its designed operating conditions. Achieving this consistently requires that a solid foundation of technological and procedural measures are put in place throughout the facility lifetime, however, these measures and efforts can erode over time without complementing them with a robust reliability culture. Having a robust reliability culture means that the organization’s values and behaviors are structured in a way that reflects that reliability is everybody’s responsibility, just like safety, and that individuals understand their role in achieving and improving reliability.
This session will cover:
- How has this been achieved at your facility?
- Any clear examples where poor reliability culture has impacted the reliability of your facility?
- How to improve and/or maintain the culture with regard to reliability?
- What are the benefits of a good reliability culture?
- What tools can be used to establish and measure this?
Particle accelerators are often associated to high energy or nuclear physics. The number of installations worldwide we can easily note that about 50% is mainly devoted to medical applications (radiotherapy, medical radioisotopes production, biomedical research). Reliability of medical accelerator facilities is considering the highest priority.
This session will discuss:
- Consideration of the medical accelerator and associated systems design; challenges and approaches of the industrial companies to achieve reliability of their products and processes.
- Medical device life cycle – Increasing accelerator reliability already during the design phase
- (industrial/medical) product life cycle
- how is industrial development done?
- how do you consider reliability during the engineering phases?
- usage of industry standards
- How to overcome the challenges of upgrading medical accelerators in operation
Reliability stems from all components working properly which requires careful monitoring, scheduled maintenance and rapid repair; these components are intricate, complex and spread across a vast area, making these tasks prone to oversight and costly in time and labour. The fourth industrial revolution, the current trend of automation and data interconnection in industrial technologies, is becoming an essential tool to boost maintenance and reliability producing advanced cutting-edge technology that are beneficial assets in this effort, like for example robotics, internet of things, machine learning, smart wireless sensors and cloud computing.
- Internet of Things devices can provide long-term, system-wide, in-situ monitoring of vital, sensitive or high-use components, and robotics enables mobile monitoring and intervention.
Machine Learning algorithms can be deployed to plan maintenance, predict potential failures and monitor degradation of components. - Robotic platforms in particular offer huge potential for accelerator and experiments maintainability. They can be deployed in radioactive environments and places otherwise harmful environments to human technicians, allowing a locally deployed robot to improve monitoring, maintenance, repair capabilities and response time by operating while accelerators are powered on, and, via teleoperation, allow the necessary experts to perform interventions regardless of their geographical location, among a wealth of additional benefits.
Novel and emerging technologies such as these represent a great opportunity to improve uptime and overall reliability of accelerators and detectors; the groundbreaking work and fruitful discussions in this workshop can help to develop the most effective ways to design and deploy these technologies to maximise their benefit.
The workshop is intended to share experiences and practices, techniques, and processes with everyone working from operations through to equipment groups improving availability of all types of accelerators. We can get our organisations a strong return on investment by working on core reliability and making informed strategic choices: a “little bit” of effort can have a significant impact on organisations Key Performance Indicators if we know what to look for, and what effort to make.
Gains in availability come from the spectrum of events; addressing the frequent root causes, as well as rare events, the effort that is to be invested in each corresponds to the expected improvement:
The four main types of institutes attending are:
- colliders/fixed target/spallation sources
- synchrotron light sources
- medical accelerators
- fusion-related machines.
There are parallels and similarities across these machines, and we can share our experiences. This session takes example institutes from these domains, asking:
- What are the KPI that concern these types of institutes?
- What examples of frequent faults are there?
- What are the recent examples of rare faults?
- What’s the availability strategy that is being followed.
At the start of the week, we all had expectations concerning the workshop, let’s discuss how well we have answered these questions.
- What was expected vs. what has been achieved?
- What were the good sessions, and what to have more of?
- What to change?
- What was missed?
We then close this session with a discussion about the disaster pictures.
This plenary discussion session will provide a forum for the exchange of ideas and best practices on a variety of reliability-related topics. The session will potentially cover a wide range of topics, including:
- The optimization of efficiency of support services and impact on reliability (e.g. electricity consumption, cooling water, etc)
- Software reliability
- Legacy equipment
- Reliability in Harsh environment
- Smart facility and reliability (digital twin)
- Automation for system configuration
The session will be structured as follows:
- Moderators will introduce a subset of the potential topics and facilitate the discussion.
- Discussions will generate topics and direction for breakout sessions.
- The audience will have the opportunity to participate in the discussion by asking questions and sharing their own experiences.
- We hope that this plenary discussion session will provide a valuable opportunity for the exchange of ideas and best practices on a variety of reliability-related topics.